Hi. We've recently had a loft conversion completed and many aspects of it look a bit iffy. This is likely be the first of many posts so please bear with me (sorry!). One thing which really bothers me is all the popped screws. There are over 60 of them that we can see. The conversion includes 3 bedrooms and a bathroom. Do we have grounds for complaint? Or can we just screw them in tighter and cover with filler?
The pictures attached show 2 where the screws have popped from under the plaster, and one where the the screw can be seen (taken inside the eaves storage area, hence no plaster).
Any comments appreciated.
The pictures attached show 2 where the screws have popped from under the plaster, and one where the the screw can be seen (taken inside the eaves storage area, hence no plaster).
Any comments appreciated.
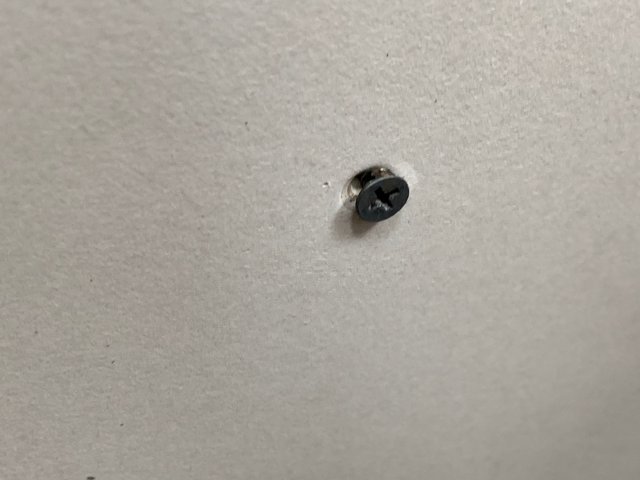

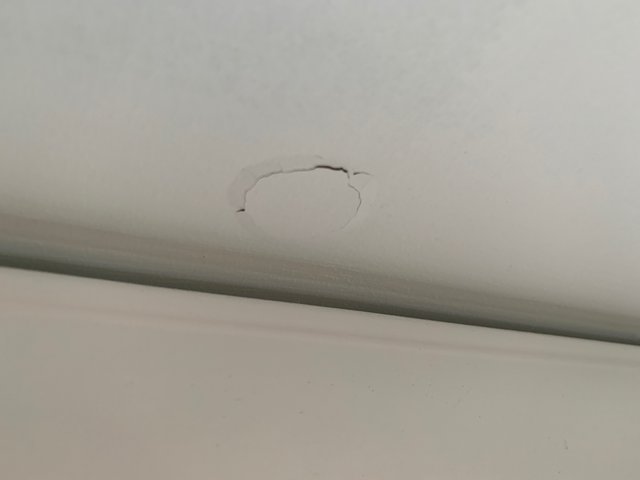